Phosphate rock is not only the 'grain' of agriculture and chemicals but also the 'green cornerstone' of the modern building materials industry. As a very important non-metallic mineral resource, it is widely distributed globally. In recent years, with the increasing demand for phosphate rock and related products across various industries, phosphate rock processing enterprises have continuously expanded their production scale. The recycling and reuse of phosphate rock processing resources are active and highly competitive, making the mining and processing technology of phosphate rock particularly important.
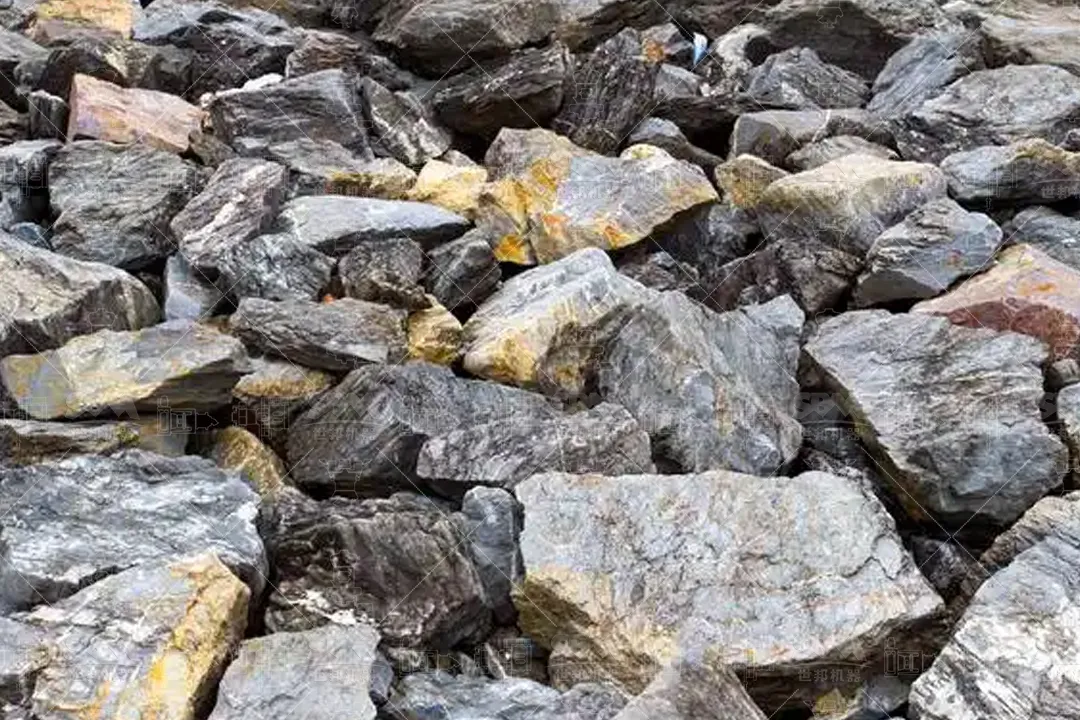
As a global manufacturer of professional grinding equipment, SBM has been deeply engaged in the phosphate processing field for over thirty years. Relying on independently developed grinding equipment and customized solutions, SBM has built multiple benchmark production lines in major phosphate-producing areas, helping enterprises achieve 'optimal use of high-quality ore and smart use of low-quality ore,' and promoting the phosphate rock industry towards intensification and intelligence.
Phosphate Rock Grinding Production Line Project
Phosphate rock has a relatively high hardness, and traditional grinding equipment faces issues such as low efficiency, high energy consumption, and severe wear during processing. A certain client plans to establish a new phosphate rock grinding production line. After three rounds of rigorous evaluation of the technical strength, service network, and industry cases of equipment suppliers, they ultimately chose SBM as their strategic partner.
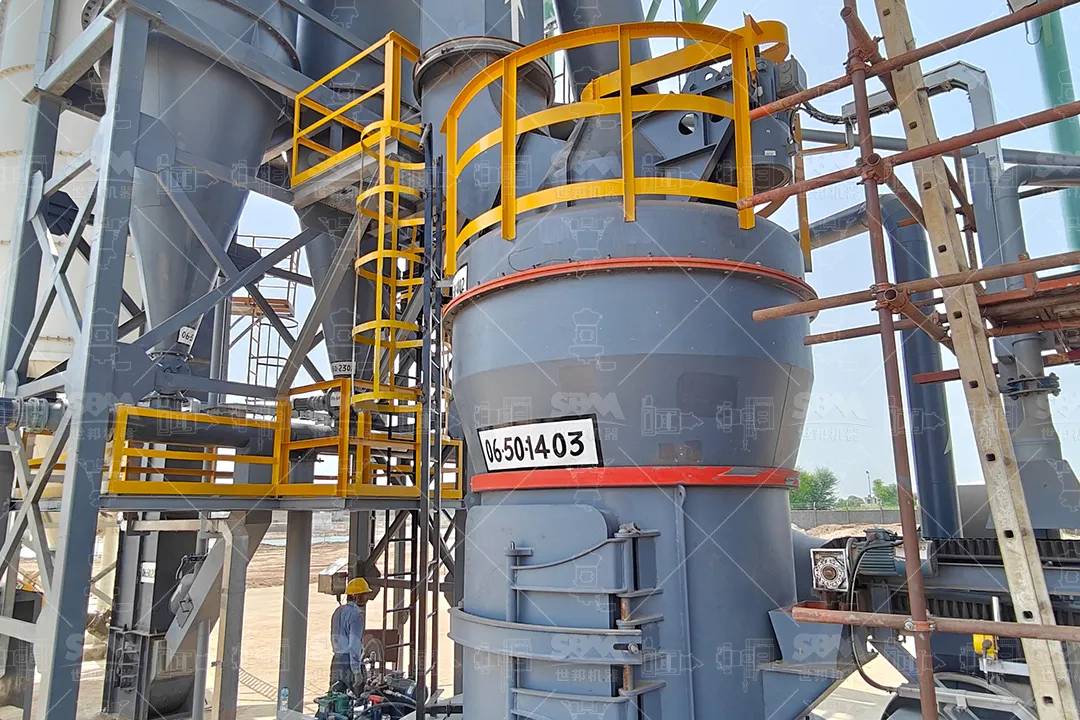
Material: Phosphate Rock
Finished Size: 200 Mesh
Application: Building Materials Industry
Equipment: MTW European Version Trapezium Grinding Mill
The client requested a balance between high output, low energy consumption, and compliance with environmental standards. SBM dispatched engineers to conduct an on-site survey, performing a comprehensive assessment of raw material characteristics and site conditions.
Based on multiple rounds of field exploration and data collection, combined with years of experience in phosphate processing, SBM designed a comprehensive lifecycle solution that includes crushing, grinding, classification, and environmental protection.
Equipment Selection
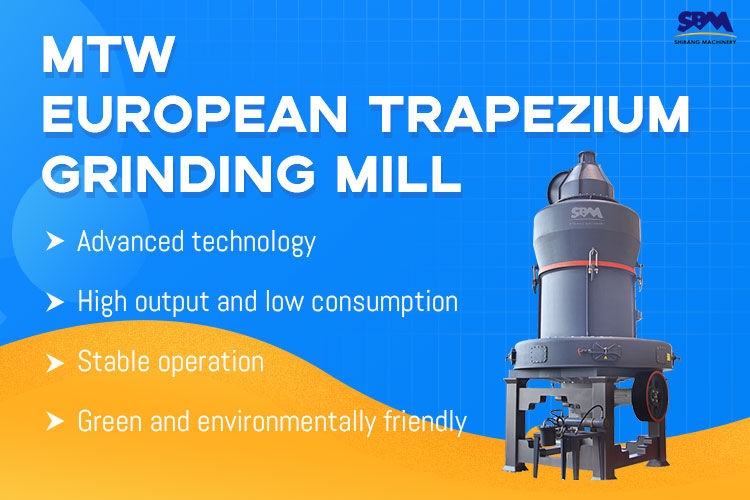
In response to the high standard requirements for phosphate rock preparation, SBM's MTW European Version Trapezium Grinding Mill operates with high efficiency. Its special structural design adapts to the client's production needs, offering high grinding efficiency, adjustable and controllable fineness, and high product purity, making it a key component of the production line.
1. Technological Iteration, Mature and Stable Equipment: SBM has nearly forty years of experience in mill manufacturing, with four generations of grinding mills undergoing iterative upgrades, leading to advanced technology and stable equipment operation.
2. Special Grinding Design, High Grinding Efficiency: The use of a curved scraper design increases the grinding working area of the material, enhancing grinding efficiency.
3. Integral Cone Gear Transmission, Reduced Energy Consumption: The adoption of integral cone gear transmission and a resistance-free air inlet design improves material flow and reduces energy consumption.
4. Thin Oil Lubrication, Extended Bearing Life: Both the main spindle drive system and the fan drive system of the equipment utilize thin oil lubrication, which has lower lubrication resistance and oil temperature compared to traditional grease lubrication, effectively extending bearing life.
5. New Type of Variable Frequency Classifier, High Product Precision: The new hanging cage classifier features variable frequency control, allowing for adjustable and controllable fineness to meet various particle size specifications.
Phosphate Rock Preparation Process Flow
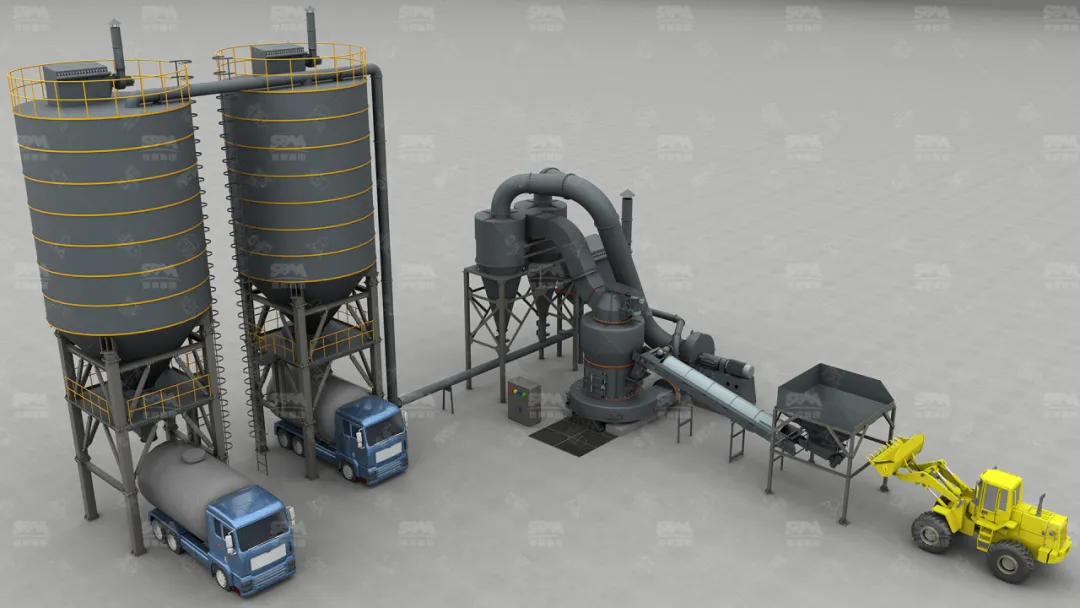
Raw materials are uniformly and continuously fed into the main grinding chamber by a variable frequency belt feeder. The ground material is then conveyed by the airflow from the fan to the classifier for grading. Under the action of the analyzer, materials that do not meet the fineness requirements are returned to the grinding chamber for regrinding, while qualified materials are transported through pipes by the airflow into the cyclone collector for separation and collection. The finished powder is discharged via the discharge device. The separated airflow is directed through the return air duct at the top of the cyclone collector back to the fan.
From Equipment Delivery to Productivity Empowerment
SBM Full-Cycle Service
Production Empowerment Training: Providing customers with specialized training in production planning, quality control, cost management, and more, helping customers improve management efficiency.
100+ Engineers for Quick Response: 24/7 online service, responding to requests within 30 minutes and dispatching engineers to the site within 72 hours, minimizing downtime losses.
In-Depth Inspections and Data Tracking: Conducting the "Quality China Tour" annually, where engineers perform equipment check-ups on-site, establish full lifecycle records, and regularly provide maintenance optimization suggestions.
“SBM's service team is like our 'technical support.” The client's technical manager remarked, ‘Whether it's an unexpected malfunction or a need for process optimization, they are always able to resolve issues promptly, truly embodying the phrase ‘ensuring worry-free production for our customers.’
The success of the phosphate rock grinding project is not only a technological validation of SBM's MTW European Version Trapezium Grinding Mill, but also a reflection of the phosphate rock industry's transformation towards high-end and green development.
In the future, SBM will continue to deepen its "Equipment + Service" strategy, leveraging powder technology as a pivot to assist global clients in achieving continuous breakthroughs in areas such as efficient resource utilization and new energy development, injecting "SBM Power" into high-quality industrial development.