Product Overview

Raymond mill is ever one classic powder grinding machine in the past. And most of modern mill are from it and MTM series milling machine is the most successful one. It optimized the inner structure and lots of core devices. Such as, the new supercharging device can greatly increase production capacity. And separated ploughs are easy to be replaced, both the spare parts cost and breakdown time are obviously reduced. According to hundreds of customers’ feedback, the MTM series grinding mills are quite good at produce 60-325mesh powders. Through word-of-mouth, this milling machine is quite hot in many countries.

Scope Of Application
Desulphurization Powder
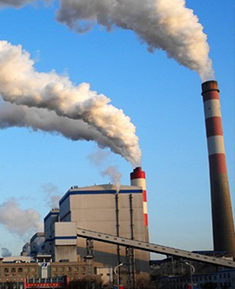
Calcium Carbonate
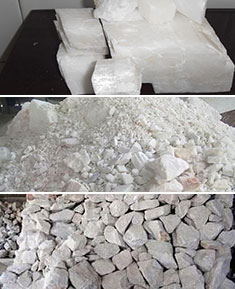
Coal Industry
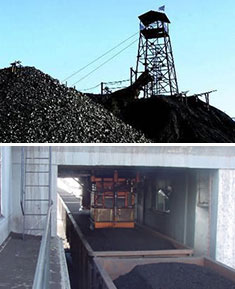
Putty powder
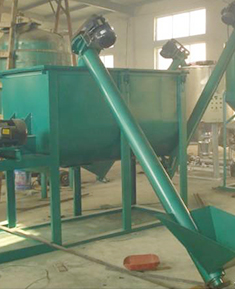
Introduction To Complete Machine Structure And Working Process
Crushed aggregates are evenly and continuously fed into the grinding cavity at fixed quantity for grinding after through the oscillating feeder.
Large materials, after crushed into expected granularity by a small jaw crusher, are sent to the bucket by the lifter.
The pulverized powder is brought by the fan flow and enters into the cyclone collector along with the air flow for separation and collection if compliant with fineness requirement.
Finally finished powders are discharged through the powder tube. The air flow is absorbed into the draft fan from the backwind tube on the top of the cyclone collector.
Introduction To Main Unit Structure And Working Process
- 1. Upper shell of classifier
- 2. Classifier belt roller
- 3. Lower shell of classifier
- 4. Tensioner
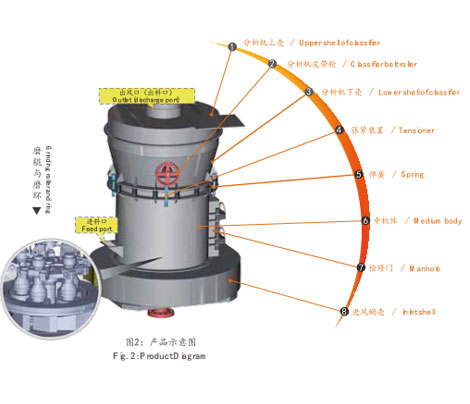
- 5. Spring
- 6. Medium body
- 7. Manhole
- 8. Inlet shell
The host drives the central shaft running (Fig. 3) by the gear box. The upper end of the shaft is connected with a wobbler spindle and the grinding roller is suspended under the wobble spindle by a cross arm shaft and forms a swinging point. The grinding roller runs along with the central shaft of the whole machine, and also rotates by friction with the grinding ring. A perching knife system is installed under the wobble spindle and feeds the material into the gap between the grinding roller and ring for pressing and grinding with the grinding roller during rotation. (Fig. 5) Air flow will bring minor powder into the powder concentrator upon entry into the grinding gravity from the bottom of the grinding ring. Coarse materials fall down and are reground; and fine powder goes into the powder collector along with the air flow and is discharged as the finished product through the powder discharge tube.
Technical Advantage
Cost advantage
It's a vertical structure and easy to be complete and covers a small area.
Creative grinding roller and ring
Extend grinding time and improve fineness and output of the finished product.
High efficient balancing and pressurizing spring
Its running pressure is 1.2 times higher than that of Raymond pulveriser under the same power condition; so the output is largely improved.
Environmental protection
Ensured by high efficient dust removal equipment and prudent component processing technologies.
High density impeller device
Under the same rotary speed, the product fineness is improved by more impellers.
High efficient saving centrifugal draft fan
while the energy saving fan, of which the impeller and the blade are pressed and formed by the tie, is at higher than 85%.
Quick adjustment and maintenance
Adjust the length of the high pressure spring, keep constant grinding force between the roller and the ring.
Main Technical Parameters
NOTE:Capacity is according to the medium hard limestone.The size,humidity level and characters of matericalswill influence the capacity.
Contact us
Fill your requirements on the following form, we will contact you as soon as possible.