Product Overview

Along with the rapid development of social economy, the requirements on pulverizing fineness by the clients from the pulverizing industry are also increasingly improved. General Raymond mill has been fairly unable to meet the demands of the market development. As a result, SCM series ultrafine grinding mill is developed. Its powders’ fineness can be adjusted within a range from 325 to 2500 meshes and its disposable fineness can reach D97≤5um which has ranked the leading level in the same trade and partial highest fineness reaching 2500 meshes through repeated experiments test by the geoscientific research institute. Because of its good performance, SCM win high praise from the users.

Scope Of Application
Paper Industry
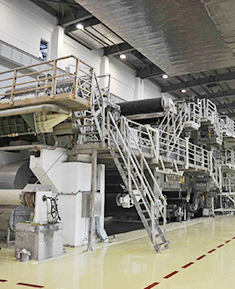
Putty Powder
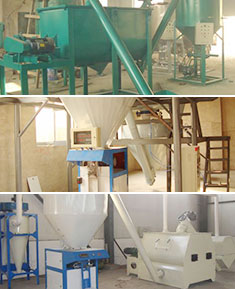
Painting Industry
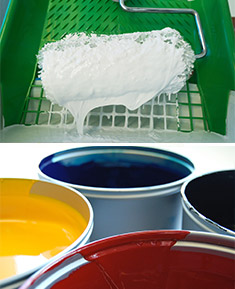
High Technology Industries
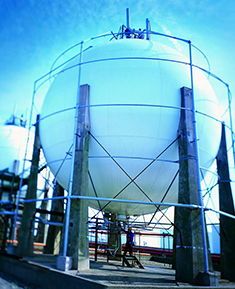
Introduction To Complete Machine Structure And Working Process
Big blocks of materials are fed into the storage bin by the elevator after being crushed into tiny particles by the hammer crusher and then materials are uniformly fed into the middle part of the upper rotary table through the feed port by an electromagnetic vibrating feeder.
Each rotary table at each layer is driven by the electric motor through inputting power into the main shaft by the speed reducer of the main engine.
Materials are scattered to the circum of the circle under the action of centrifugal force and fall into the roller path of the grinding rings and then punched, pressed, grinded and crushed by the rolling mill and materials will afterwards fall into the second and third layers to be further crushed through after the first layer crushing.
The high-voltage centrifugal fan aspirates external air into the machine cavity and feeds the materials through three layers crushing into the powder concentrator. The spinning turbine in the powder concentrator will make the nonconforming coarse particles fall back and re-grinded and the fine powder will become the finished products by entering into the whirlwind powder collector along with the airflow.
Introduction To Main Unit Structure And Working Process
- 1. Hammer Crusher
- 2. Hoister
- 3. Storage Bin
- 4. Vibratory Feeder
- 5. SCM Main Engine
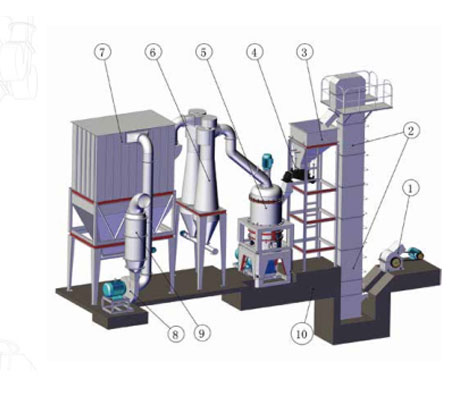
- 6. Powder Collector
- 7. Pulsed Jet Filter
- 8. Fan
- 9. Silencer
- 10. Foundation
Main unit’s working process
Each rotary table at each layer is driven by the electric motor through inputting power into the main shaft by the speed reducer of the main engine. Three layers’ ring roller rolls and rotates in the roller path of the grinding rings.
When materials are uniformly fed into the center of the upper rotary table, they are scattered to the circum of the circle under the action of centrifugal force and fall into the roller path of the grinding rings and then punched, pressed, grinded and crushed by the rolling mill and materials will afterwards fall into the second and third layers to be further crushed through after the first layer crushing.
Finally, the fine powder will become the finished products by entering into the whirlwind powder collector along with airflow and via a discharge valve at its bottom while the airflow with few fine dusts will be purified by the pulsed jet filter and discharged through the fan and silencer.
Technical Advantage
High Output and Low Energy Consumption
40% higher than that of a jet mill or a stirred mill and capacity of a ball mill while its system energy consumption is only one-third of
High Fineness
Product fineness can be arbitrary adjusted within a range from 325 to 2500 meshes and its disposable fineness can reach D97≤5um
Safe and Reliable
There is no rolling bearing and bolts in the mill chamber.
Heavy rotor design and tight test method
The application of the pulsed jet filter and silencer has reduced the dust pollution.
Safe Operation and Low Operating Costs
Operators can finish most of work through the electric control system. As a result, the labor cost is quite low.
High Output and Low Energy Consumption
40% higher than that of a jet mill or a stirred mill and capacity of a ball mill while its system energy consumption is only one-third of
High Fineness
Product fineness can be arbitrary adjusted within a range from 325 to 2500 meshes and its disposable fineness can reach D97≤5um
Safe and Reliable
There is no rolling bearing and bolts in the mill chamber.
Heavy rotor design and tight test method
The application of the pulsed jet filter and silencer has reduced the dust pollution.
Safe Operation and Low Operating Costs
Operators can finish most of work through the electric control system. As a result, the labor cost is quite low.
Main Technical Parameters
NOTE:Capacity is according to the medium hard limestone.The size,humidity level and characters of matericalswill influence the capacity.
Contact us
Fill your requirements on the following form, we will contact you as soon as possible.