Product Overview

In the ultrafine powder grinding field, LUM series ultrafine vertical roller mill is another excellent product besides SCM series super-micro mill. Though both of them are able to produce 425-2500mesh powders, they have some differences. If we use one set LUM vertical roller mill produce 425-1350 mesh powders in one hour, the capacity is 6-8 times than that of SCM series super-micro mill. Because the LUM has outstanding performance in the pulverization of while ultrafine-non-metallic ore, it has been widely used plastic, papermaking, PVC, printing ink, coating and pigment and many other industries.

Scope Of Application
Paper Making Industry
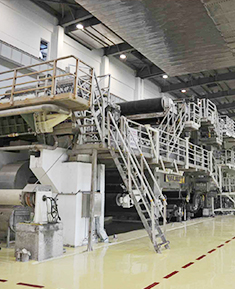
PVC Industry
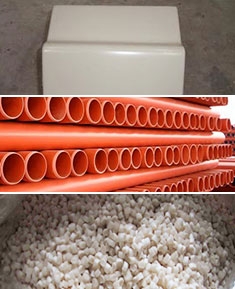
Painting Industry
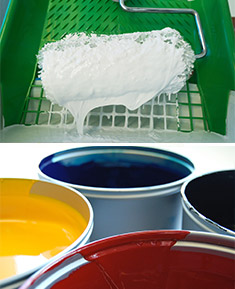
Plastic Industry
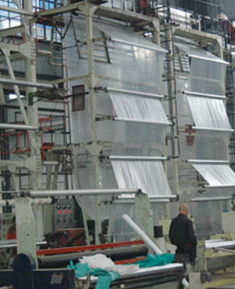
Introduction To Complete Machine Structure And Working Process
When the raw materials enter into the grinding cavity, all pulverizing works are finished there, including the powder classifying.
Raw materials fed to hopper are lifted up by elevator and fed to the grinding mill evenly and constantly.
After the classifying work, powders are collected and the whole processing work are usually finished. But to many producers, it’s not enough.
If producers want to produce finer powders, they can use the secondary classifying system. Through this system, the fineness can reach 2500mesh and even much more finner.
Introduction To Main Unit Structure And Working Process
The grinding plate is rotated by the main motor via the reduction gear. Meanwhile, air enters the mill interior via the air inlet. The screw conveyor is responsible for conveying materials. Materials then fall onto the center of the grinding plate in rotation. Due to the centrifugal force, the materials evenly move from the center of the grinding plate towards its fringe. While passing across the track in the grinding plate, large blocks of materials are crushed and ground directly by the grinding roller. The fine particles from the material bed, owing to squeezing, where the inter-particle crushing takes place.
The crushed materials continue to move towards the fringe of the grinding plate until they are taken away by strong air ring. While the materials along with the air flow pass through the separator located above the grinding plate, the coarse particles return to the grinding plate for re-pulverization due to the action of the action of the rotor blade; the fine particles along with the air flow leave the mill interior and are collected and discharged as finished powder product by the powder collector.
When moving together with the materials to the fridge of the grinding plate, due to its weight, the tramp iron cannot be raised by air flow but falls into the lower mill chamber and then is scraped into the slag outlet to be discharged by the scraping plate. This efficiency ensures the quality of finished powder product.
Technical Advantage
High Efficiency & High Quality Product
The grinding curves of the roller shell, liner plate and pre-compaction device are special designed.
Advanced Separation Technology
The use of PLC control system. And the use of ultrafine pulverization and multi-rotor separation can save energy by 30%-50%.
Intelligentized Control System
Besides the PLC control system, the applied limit device and the separated lubrication system make the machine work much more steady and safety.
Easy Maintenance & Low Operation Cost
The grinding roller don’t directly contact with the grinding plate, therefore these parts have long service life.
Environmentally Friendly
Special structural design and operating principle of the mill ensures substantial reduction of vibration hence noise level.
Main Technical Parameters
NOTE:Capacity is according to the medium hard limestone.The size,humidity level and characters of matericalswill influence the capacity.
Contact us
Fill your requirements on the following form, we will contact you as soon as possible.