Introduction to mill
A grinding mill is a piece of equipment used to convert materials from lumps or granules into powder. There are many classifications of grinding machines. According to the size, there are small laboratory grinding mills, large grinding mills, etc. According to the usage, it can be divided into agricultural grinding mill and industrial grinding mill. In terms of appearance and function, it can also be divided into ball mill, vertical mill, Raymond mill, high-pressure suspension roller mill, European version mill, trapezoidal mill, micro powder mill, coarse powder mill, etc.
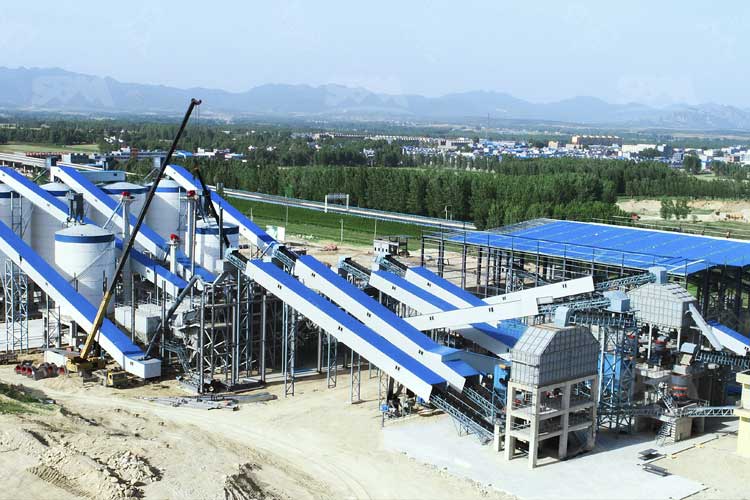

Laboratory grinding mill is also called small grinding mill. It is a kind of test equipment specially used in laboratories. Its main features are small size, light weight and multi-purpose. Used to study the crushing, grinding and homogenization of substances. It uses the principle of mechanical grinding to mix and grind the sample into fine particles or powder through high-speed rotating grinding discs and grinding rods. Experimental grinding mills are widely used in experimental research in materials science, chemical pharmacy, biomedicine and other fields. Large grinding mills are suitable for industrial production, and are generally related to mining, sand and gravel, construction and other industries. The most widely used ones are gravel mill, construction waste crushing, etc.
The grinding principles of agricultural mills and industrial mills are basically the same. After the materials are cut, extruded, collided, and crushed to the required particle size, the materials are sent to the storage hopper by the elevator, and then the materials are conveyed by the vibrating feeder. It is evenly and continuously fed into the main grinding chamber of the grinding mill. Due to the centrifugal force during rotation, the grinding roller swings outward and presses against the grinding ring. The scraper scoops up the material and sends it between the grinding roller and the grinding ring. Due to the rolling of the grinding roller, To achieve the purpose of crushing. The fine powder after grinding the material is brought into the analysis machine with the circulating air of the blower for sorting. The too fine and coarse material falls back to be reground. The qualified fine powder enters the finished product cyclone powder collector with the air flow and is discharged through the powder outlet pipe. That is the finished product. The difference is that because the material of the agricultural grinding mill is soft, the extrusion pressure and material requirements are relatively low. Industrial grinding mills are different. Industrial materials generally have higher hardness, such as barite, limestone, ceramics, slag, etc., which require much higher equipment strength.
The historical development and evolution of grinding mill
In ancient times, smart humans invented mills. A mill is a grinding tool that is manually shaken or driven by animals. It is mainly used in agricultural production, such as making flour. Later, with the advancement of human civilization, mills designed by natural science that used wind and water power were produced, such as windmills and waterwheels. Mills that used wind and water power to drive the rotation of the millstone to grind grains appeared. Later, the Industrial Revolution brought revolutionary changes to productivity, and mills driven by steam engines appeared, which greatly improved production efficiency. In modern times, electricity has become dominant, and various large-scale grinding mills are driven by electricity, which not only has high production efficiency, but is also environmentally friendly and energy-saving. Provides guarantee for the construction of modern civilization.

importance in various industries
Nowadays, grinding mills play a vital role in every aspect of our life and production. First of all, flour mills can be used to make a variety of flours, pastes, powders, condiments, etc. in the food processing industry. For example: wheat flour, corn flour, oatmeal, tahini, peanut butter, etc. The advantage of the grinder is that it can grind out extremely fine powder. The powders have strong adhesion and are not easy to scatter. The food tastes more delicate.
Secondly, in the cosmetics industry, grinding machines can be used to grind various natural raw materials, such as pearl powder, loess, aloe vera powder, etc., to make skin care products, facial masks, pigments, etc. The advantage of the grinder is that it can grind the raw materials into finer powder, making it easier to be absorbed by the skin, increasing the efficacy and effect of the product.
Thirdly, in the pharmaceutical industry, grinding mills can be used to make various pharmaceutical powders, such as Western medicine, Chinese medicine, health products, etc. The advantage of the grinder is that it can grind the medicine into a finer powder, making the medicine more easily absorbed by the body and enhancing the efficacy of the medicine.
Fourth, the grinding mill also plays an extremely important role, which is used in industrial production. We all know that our lives cannot be separated from high-rise buildings and highways. Building these requires building materials, which come from equipment such as crushing and grinding machines.
Classification of industrial grinding machines
- Ball mill. It got its name because of its round shape. It is widely used in the mineral processing industry. There are two grinding methods: dry grinding and wet grinding. According to the different ways of discharging ore, it can be divided into grid type and overflow type.
- Vertical grinding mill. Also called vertical mill or vertical mill, it is a new type of energy-saving and consumption-reducing production line equipment. It has more advantages than other similar production line equipment in terms of energy consumption and environmental protection, and the production output of a single unit is compared with the fineness of the produced powder. Significantly improved, it is an energy-saving and consumption-reducing production line equipment advocated in our country.
- Raymond mill. It is also known as Raymond mill and Raymond machine. Raymond mill can be said to have a very long history. It is the earliest model of grinding equipment in the industrialization process. So far, it has the largest share in the production line. It's also very big. With the development, the Raymond mill has also been updated several times. Compared with the old equipment, the transformed Raymond mill has a higher screening rate of 99%, and adopts a centralized control system to transform the traditional The manual Raymond grinding mill has been improved to become a highly automated equipment.
- High pressure suspension roller mill. Also known as high-pressure mill and suspension roller mill, this equipment can grind materials with higher hardness. It can grind materials below Mohs grade 9.3 very well. After modification, the final fineness of this model can reach up to 1000. About the mesh, and the fineness can be freely adjusted between 0.613mm and 0.33mm, making it more adaptable.
- European version mill. This equipment is relatively large. Because its design principle is based on the advanced technology of European mills, it is called the European version of the mill. After improvements, this equipment has smaller energy loss and higher efficiency. It is a large-scale equipment.

- The trapezoidal mill can be said to be a new type of equipment developed on the basis of high-pressure grinding. It has been improved according to the needs of the majority of powder manufacturing companies, and the shortcomings of the original equipment have been eliminated to make it more suitable for user needs. .
- Micro-powder mill is also what we often call ultra-fine grinding. Under the same fineness conditions, the price is less expensive than traditional air-flow mill. The fineness of the finished product can reach 3000 mesh. There are fewer production links and it is suitable for ultra-fine powder processing. Enterprise use.
- Grind coarsely. Also called swing-up grinding mill, it is a new type of equipment developed on the basis of traditional grinding equipment. It can be used to process relatively fine sand. The quality of the products processed by this equipment is the best for making building materials. Excellent, it solves the user's need for processing mixed materials below 3mm.
Working principle and mechanism of grinding mill
The grinding process of the grinding mill is divided into three stages. The first stage of cutting is the beginning of all stages. As a rock-cutting process, chipping sets the stage for subsequent steps in mineral processing operations. Whether it is surface or underground mineral deposits, they must go through this step before becoming grinding materials. Then you can move on to the next stage!
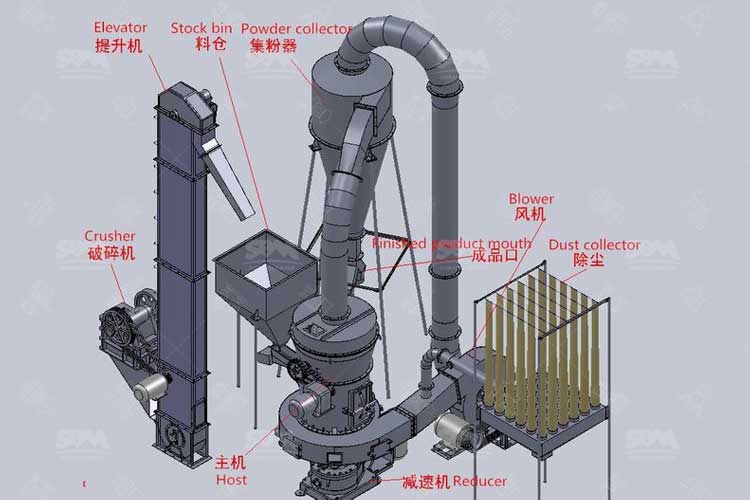
The second stage is crushing and screening. After the first stage, the size of the ore material is significantly reduced and can be processed using finer crushing equipment. Different types of crushers are used for processing according to various established size, shape and strength parameters.

The third stage is grinding. After the second stage of crushing, we hope to further process the ore to obtain mineral powder. Size reduction can occur for a variety of reasons, we may want to release individual minerals trapped in the ore, or simply expose the minerals to a leaching solution. Grinding can be dry or wet. Simply put, it either does not require water for processing, or water is used during ore processing. Wet grinding is usually preferred because of its lower power consumption and higher grinding capacity. And it’s more environmentally friendly. If there is concern that wet grinding will change the physical or chemical structure, or if a higher percentage of fines is required, dry grinding must be used.
Grinding processes of different types of mills
Semi-autogenous mill/SAG mill (primary mill). These mills use grinding balls inside, and there are friction, impact and abrasion forces between the grinding balls and the ore particles, resulting in finer particles. Feed size range is 400 mm/16 inches and product size is 75 microns. Large SAG ground products are either finished sizes ready for machining or direct sizes for further grinding. Examples include applications in gold, copper and platinum mines, as well as applications in the lead, zinc, silver, alumina and nickel industries.
Rod mill. These rotary mills use rods as grinding media internally, causing friction and wear between the steel rods and the ore particles. The rod mill accepts feed material up to approximately 50 mm (2 inches) and produces a product size of 600 microns. Rod mills are better suited for crushing large pieces of ore due to the heavier weight of the rods. Includes large chunks of rock, coal, copper, or other media. The product will become fine aggregate for use in the construction materials and chemical industries. Additionally, it is ideal when grinding coarse-grained ores.
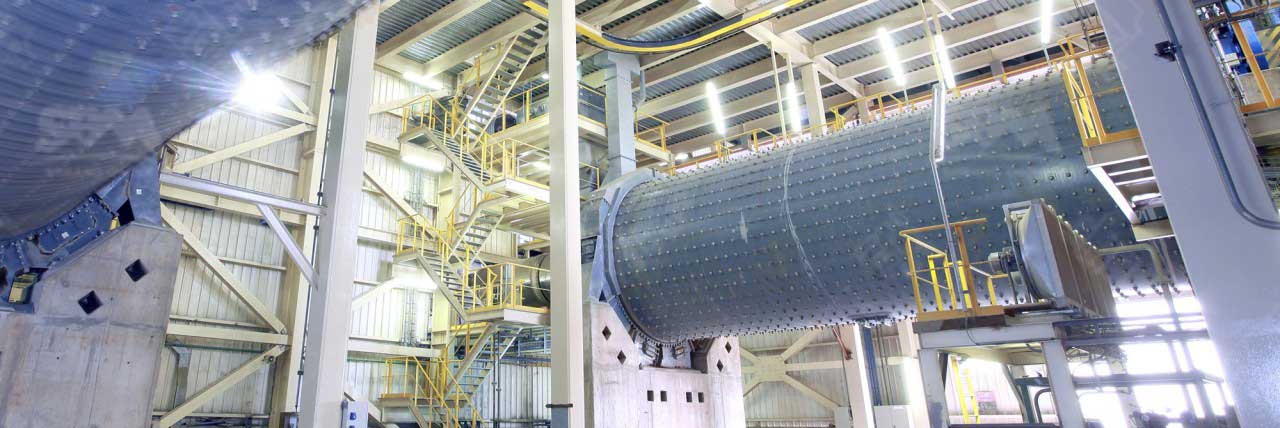
Ball mill. Balls are used as grinding media to break coarse feed materials into extremely fine powder through impact and friction. Ball mills use feeds of about 15 mm (0.5 in) or finer and the product size is so fine that no practical grinding limit is specified. Examples include applications in mineral processing, paints, pyrotechnics, ceramics and selective laser sintering. It is widely used in powder production lines for cement, silicate, refractory materials, fertilizers, glass ceramics, etc., as well as in ferrous metal and non-ferrous metal mineral processing.
Types of Mill Operations
From the perspective of the operation type of the grinding mill, grinding mills are divided into the following categories.
- 1. Scraper grinder. This type of grinder uses a scraper to scrape the material into the grinding disc for grinding. During operation, put the material into the feed port of the machine, then start the machine, and the scraper will scrape the material into the grinding disc. This method is suitable for grinding harder materials.
- 2. Pendulum mill. This machine uses an oscillating hammer head to crush and grind materials. During operation, the material is put into the feed port of the machine, and the pendulum will rotate and swing at a high speed, crushing and grinding the material during the collision with the grinding disc. This method grinds materials that are harder and require controlled grinding particle size.
- 3. Air flow mill. Airflow mills use high-speed airflow to crush and grind materials. The high-speed air flow will bring the materials from the feed port to the center of the grinding disc for grinding. Suitable for materials with soft texture and grinding particle size requirements.
- 4. High-speed centrifugal mill. This machine uses the centrifugal force generated by the high-speed rotating grinding disc to project the material from the material port to the edge of the grinding disc for grinding. This method is suitable for materials with hard materials and the grinding particle size can be controlled.
Grinding Mill Applications and Industries
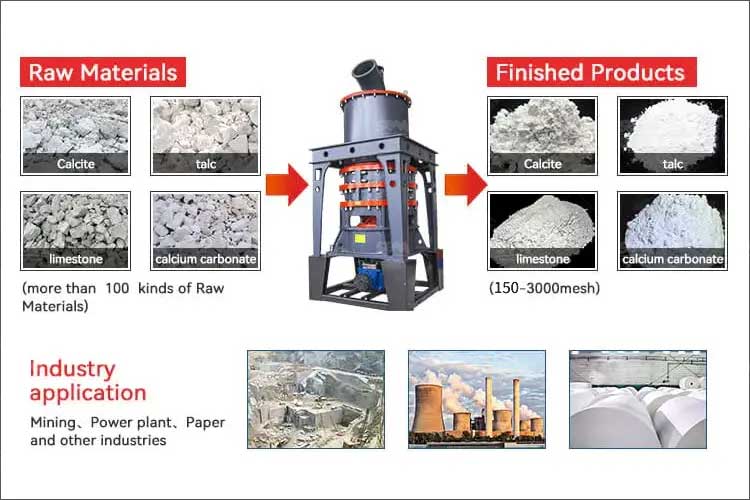
The application of grinding mill is inseparable from our daily production and life. Among them, the ore grinding industry is the most widely used. Ore grinding machines are used to grind various ores and mineral materials into powder or fine particles for further utilization in mineral processing and other industrial fields. With the continuous development of technology and the gradual depletion of ore resources, the multiple applications of ore grinding machines have become a new choice in the field of mineral processing, which not only improves the comprehensive utilization rate of resources, but also promotes environmental protection and sustainable development. Especially its wide application in ore grinding and mineral powder preparation provides guarantee for the production of coatings, ceramics, glass, rubber and plastic products. Also, in the production of energy materials such as pulverized coal and coke for use in power generation, metal processing or other industrial processes. This helps improve energy resource utilization efficiency. In addition, grinding mills also play an irreplaceable role in the pharmaceutical and chemical industries and food processing. Mainly used to prepare granular drugs, such as granules and capsules. Used in the preparation of food products such as flour, coffee powder, spice powder and chocolate powder.
Mining and beneficiation applications
In the entire mineral processing and milling production chain. The grinding mill plays an irreplaceable role. First, mining equipment is used to extract materials from the mining area and preliminarily screen them out. Then there is mineral processing equipment to crush and select the materials to obtain materials suitable for grinding. Finally, grinding equipment is used to make powder. It can be seen from this. Grinding equipment plays an indispensable role in the entire mining and mineral processing production. Without grinding equipment, the powder materials needed for industrial production and daily life cannot be obtained.
Mills in cement manufacturing

The process of cement manufacturing is that the material enters the first chamber of the ball mill evenly and spirally from the feeding device through the feeding hollow shaft. There are ladder linings or corrugated linings in the chamber, and steel balls of different specifications are installed inside. The rotation of the cylinder generates centrifugal force to push the steel balls. It is brought to a certain height and then dropped, causing heavy impact and grinding to the material. After the materials reach coarse grinding in the first chamber, they enter the second chamber through the single-layer partition plate. This chamber is equipped with a flat lining plate and contains steel balls for further grinding the materials. The powdery material is discharged through the discharge grate plate to complete the grinding operation.
Advantages of grinding mill
Effective particle size reduction in grinders
Effective particle size reduction in a grinder often requires consideration of a range of factors, including the type of grinder, operating parameters, nature of the feedstock, etc. Increasing grinding time can improve particle fineness, but care needs to be taken to avoid overgrinding to prevent overheating and damaging the material. Use appropriate grinding media such as steel balls, ceramic balls, etc. to ensure effective grinding action. Smaller media are generally more efficient at fine grinding. Reduces friction and heat, helping to prevent overheating. For some sticky materials, adding a dispersant can help disperse the particles better. Proper pretreatment of raw materials to ensure uniform particle size will help improve the grinding effect.
Mill energy efficiency and reduced power consumption
Improving the energy efficiency of grinders and reducing power consumption are environmentally friendly and economically feasible goals. Use efficient electric motors to replace traditional electric motors with higher energy consumption. Flexibly adjust the motor speed as needed to reduce unnecessary energy consumption. Install an intelligent control system that can monitor and adjust the operating status of the grinder to ensure it operates at the optimal working point. Utilize advanced automatic control algorithms to adjust parameters in real time according to changes in working conditions, improve system response speed, and reduce unnecessary energy consumption. Choose appropriate grinding media, such as high-density, high-hardness media, to reduce friction losses. Replace the grinding media regularly to avoid increased energy consumption due to excessive wear. Optimize the design of the cooling system to ensure efficient heat dissipation and reduce energy consumption. Consider recovering energy during the grinding process, such as through a waste heat recovery system, to use a portion of the waste heat for heating or other energy needs. Use sensors and monitoring systems to monitor equipment operating conditions in real time and promptly discover and repair abnormal energy consumption issues.
Mill care and maintenance
Clean impurities and dust inside and outside the equipment to prevent them from affecting the normal operation of the equipment. Pay special attention to cleaning wear parts such as grinding discs, grinding media and screens to ensure grinding results.
- 2. Check the lubrication system:
Check the lubrication system regularly to ensure that the lubricating oil or grease is sufficient and working properly. Replace lubricating oil or grease according to the frequency of use and pressure requirements of the equipment.
- 3. Check the transmission system:
Regularly inspect the drive system, including belts, chains, gears and other parts, to make sure they are not loose, worn or damaged. Adjust or replace severely worn transmission parts to ensure normal transmission.
- 4. Replacement of worn parts:
Regularly check worn parts, such as grinding media, grinding discs, etc., and replace them in time according to wear conditions. Pay attention to regular inspection and replacement of seals to prevent oil leakage or dust entry and maintain the sealing of the equipment.
- 5. Electrical system inspection:
Regularly check electrical systems, including cables, connectors, switches, etc., to ensure they are safe and reliable. Check the insulation of the motor to ensure that the motor is working properly.
- 6. Cooling system inspection:
Check the cooling system regularly and clean the radiator to ensure good cooling effect. Check the level and quality of the coolant and replace aged or contaminated coolant promptly.
- 7. Automation system maintenance:
For mills with automated systems, regularly check and calibrate sensors, instruments and controllers to ensure their accuracy and reliability. Update the control system software to ensure proper cooperation with the equipment.
Environmental impact of mills and improvement measures
Mills have a range of environmental impacts that depend on a variety of factors, including the type of equipment, how it is used, the nature of the raw materials, etc.
- 1. Mills usually require a large amount of electrical energy during operation, especially in the processing of high-energy-consuming materials. We reduce energy consumption by using efficient motors, improving the grinding process, and introducing energy recovery systems.
- 2. The grinding process may cause wear and tear of raw materials and the generation of waste. We strictly select wear-resistant materials, use renewable raw materials, and implement waste treatment and recycling.
- 3. The operation of the grinder may produce noise and vibration, which may adversely affect the surrounding environment and the health of workers. We use sound insulation and vibration damping devices and take engineering measures to reduce the transmission of noise and vibration.
- 4. The cooling system may produce a large amount of waste water, which puts a certain amount of pressure on water resources. To address this problem, we optimize the cooling system and adopt a closed-loop cooling system for wastewater treatment and recycling.
The future development direction of grinding mills
As countries have increasingly higher requirements for environmental protection and restrictions on carbon emissions, the preparation of future mills must not only meet environmental protection requirements. We should also pay more attention to our own environmental innovation and low-carbon production. To develop the era of innovative mill 4.0. Our mine production must not only meet the basic functions of grinding and grinding. We also need to create ecological construction of mines. It is necessary to realize new forms of green mines, low-carbon mines, tourist mines, and diversified mines.