Cement is a fundamental building material used globally for constructing homes, infrastructure, and various structures. At the heart of cement manufacturing lies a critical process – the grinding of clinker, cement raw materials, and other minerals into a fine powder. This process is accomplished through the utilization of grinding ball mills, which play a pivotal role in the production of high-quality cement.
The Cement Manufacturing Process
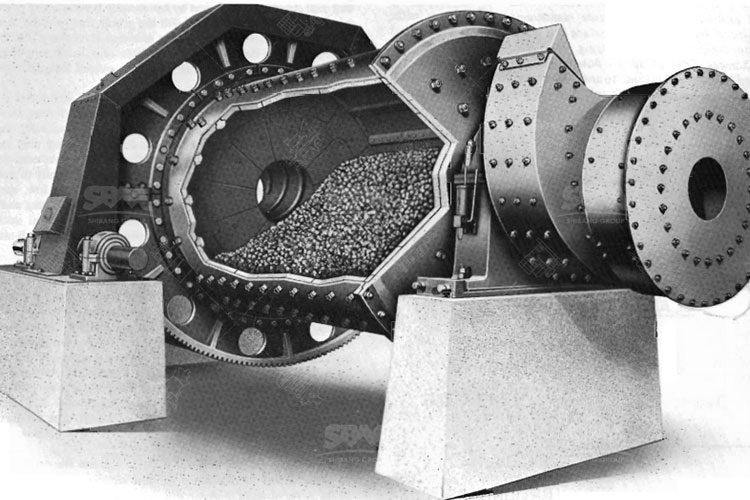
Before exploring the role of grinding ball mills, it is essential to understand the broader context of cement manufacturing. The process can be broken down into several key stages:
Raw Material Preparation:
Raw materials such as limestone, clay, shale, and silica are extracted and transported to the cement plant. Crushers reduce these materials into smaller pieces.
Raw Material Grinding:
The crushed raw materials are blended to form a consistent raw meal. This raw meal is then fed into grinding mills to be pulverized into a fine powder.
Clinker Production:
The ground raw meal undergoes high-temperature processing in a kiln, resulting in the formation of clinker. Clinker is cooled and then ground with gypsum in a cement mill.
Cement Grinding:
The final step involves grinding the clinker into a fine powder. This is where grinding ball mills come into play.
Role of Grinding Ball Mills in Cement Manufacturing
Grinding ball mills are cylindrical devices used to grind and blend materials for use in mineral dressing processes, paints, pyrotechnics, ceramics, and selective laser sintering. In the context of cement manufacturing, these mills are employed to reduce the clinker and other materials to a fine powder. The effectiveness of this grinding process directly impacts the quality and properties of the final cement product.
Principle of Operation:
Grinding ball mills operate on a simple yet effective principle. The material to be ground is fed into the mill, and as the cylinder rotates, the grinding media (typically steel balls) crush and grind the material into a fine powder. The rotation of the mill is facilitated by motors, and the grinding process continues until the desired fineness is achieved.
Types of Grinding Media:
The choice of grinding media is crucial in determining the efficiency of the grinding process. Steel balls are commonly used due to their durability and effectiveness in breaking down materials. However, other types of media, such as ceramic balls or cylpebs, may be used based on specific requirements and the nature of the material being ground.
Energy Efficiency:
The efficiency of grinding ball mills is a critical factor in cement manufacturing. Advancements in technology have led to the development of more energy-efficient mills. High-efficiency separators, optimized grinding media distribution, and innovative mill designs contribute to reducing energy consumption, a key consideration in the sustainable production of cement.
Technological Advancements in Grinding Ball Mills
Over the years, technological advancements have played a significant role in enhancing the performance and efficiency of grinding ball mills in cement manufacturing. Some notable developments include:
Vertical Roller Mills (VRM):
VRMs have gained prominence as an alternative to traditional ball mills. They feature a vertical orientation, allowing for more efficient grinding and better utilization of energy. VRMs are particularly effective in grinding materials with high abrasiveness.
Use of Alternative Fuels:
Cement manufacturers are increasingly incorporating alternative fuels in the grinding process. This not only addresses environmental concerns but also contributes to cost reduction. The use of alternative fuels necessitates adjustments in the grinding process to accommodate variations in fuel properties.
Smart Grinding Systems:
The integration of smart technologies, such as automation and data analytics, has revolutionized the operation of grinding ball mills. Real-time monitoring, predictive maintenance, and process optimization contribute to increased efficiency and reduced downtime.
Advantages and applicability of ball mills
The ball mill has efficient grinding performance to ensure that the cement reaches the required particle size and surface area. In addition, the ball mill has good adaptability to different types of clinkers and raw materials, as well as its adjustability under different production conditions.
Increase filling rate and rotation rate
The processing capacity of the ball mill increases as the filling rate of the steel balls increases. Increasing the filling rate increases the probability of the steel balls crushing the ore and the self-grinding effect of the ore. When the steel ball filling rate is 45%, the load of the ball mill is maximum. When it exceeds 45%, the load decreases significantly as the filling rate increases. This is mainly because as the filling rate increases, the throwing point of the steel ball is raised, and the impact point of the falling steel ball accelerates closer to and exceeds the center of rotation, and its resultant moment is greatly shortened and becomes O to a negative value. The load required for the resultant moment of impact caused by the falling steel ball (containing minerals) changes from large to 0, until it becomes the driving force to push the cylinder to rotate (that is, the point of action of the resultant force exceeds the center, and the resultant moment is negative).
Challenges and Future Trends
While grinding ball mills are indispensable in cement manufacturing, the industry faces various challenges and continues to evolve. Some of the key challenges include:
Environmental Impact:
Cement production is associated with significant environmental impact, primarily due to the high energy consumption in the grinding process. Sustainable practices, including the use of alternative fuels and energy-efficient technologies, aim to mitigate these concerns.
Carbon Neutrality:
The cement industry is actively exploring ways to achieve carbon neutrality. This involves not only optimizing grinding processes but also investing in carbon capture technologies and exploring alternative cementitious materials.
Circular Economy:
Embracing a circular economy model involves recycling and reusing waste materials. Grinding ball mills can contribute to this initiative by incorporating recycled materials in the cement production process.
Innovations in Grinding Aids:
Grinding aids, chemicals that enhance grinding efficiency, are continually evolving. Innovations in grinding aids aim to improve overall performance, reduce energy consumption, and address environmental concerns.
Grinding ball mills stand as the workhorses of the cement manufacturing process, tirelessly transforming raw materials into the essential building material that is cement. As technology advances and the industry embraces sustainability, the role of grinding ball mills continues to evolve. From the integration of smart technologies to the quest for carbon neutrality, the cement industry is poised for a transformative journey, where grinding ball mills will play a pivotal role in shaping its future.